What is Lead time in Inventory Management- A Getting Started Guide
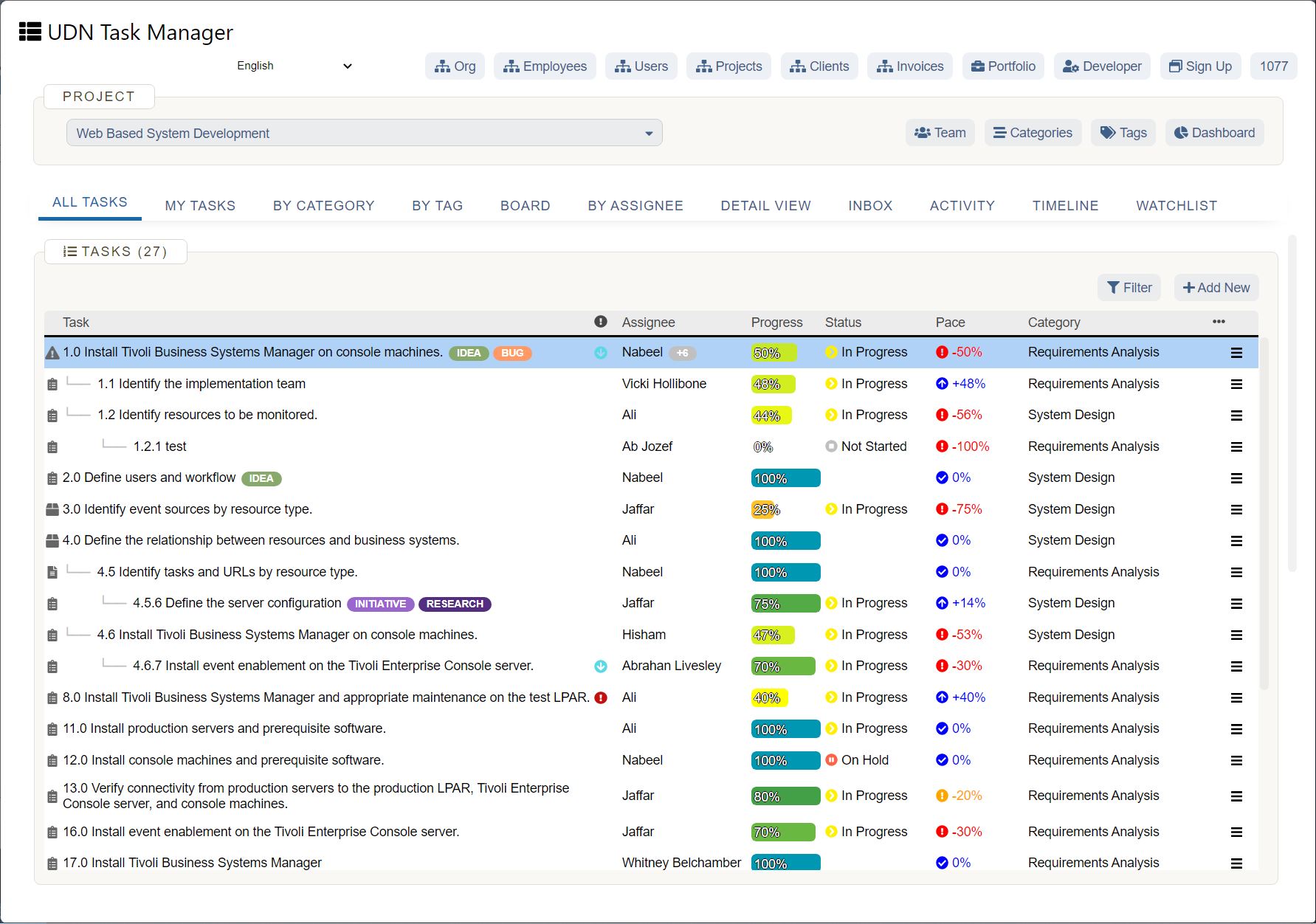
We all know how important time is, once lost it can never be turned back. Similarly, we are all familiar with how time management can play an important role in any person’s, company’s, or project’s success.
The concept of lead time in inventory management revolves around the same concept. Let’s look into what lead time actually is, how you can calculate lead time, and its applications and importance.
What is Lead Time in Inventory Management?
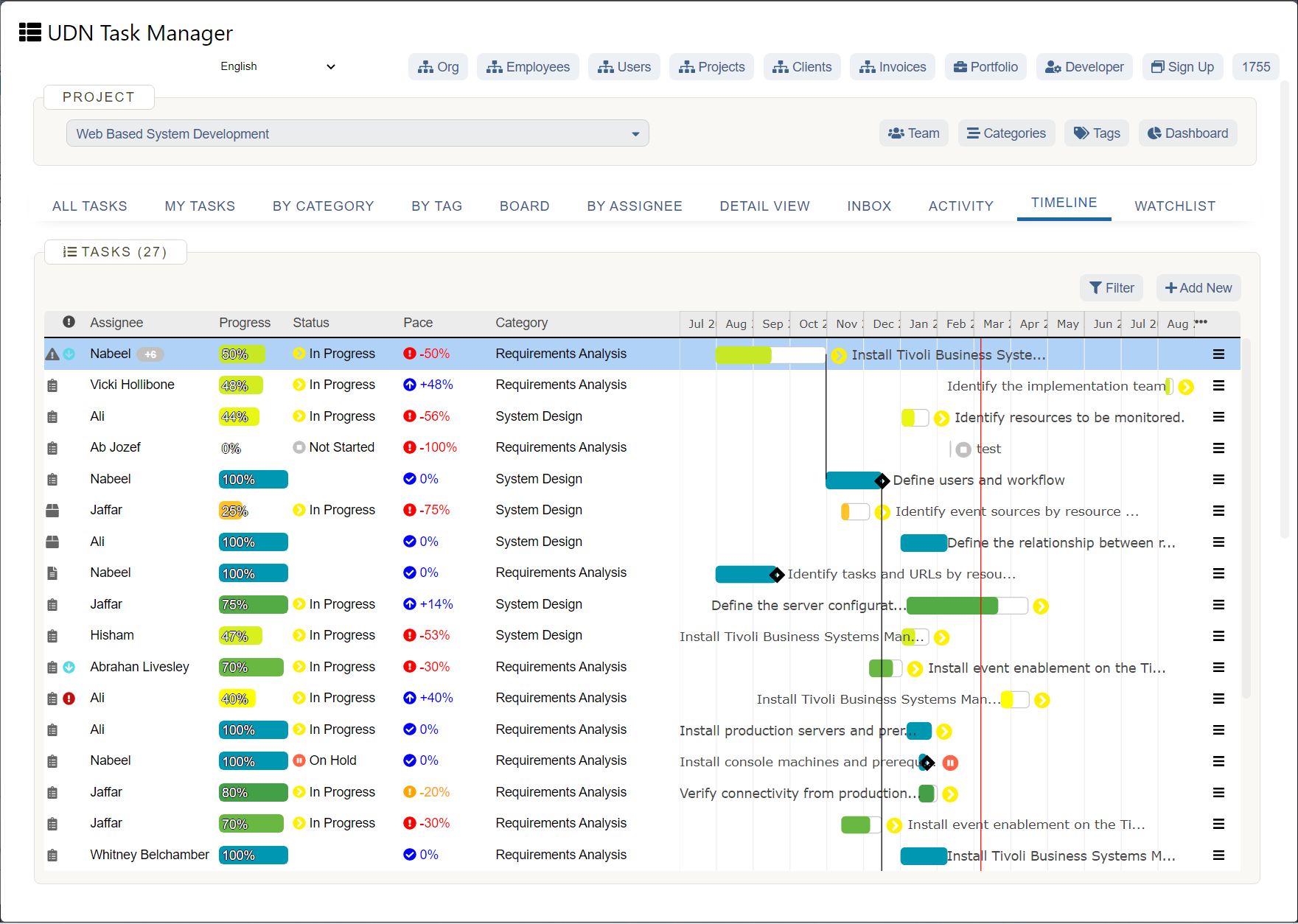
Simply put, lead time stands for the time taken from the start of any task to its completion. Its most common application is for supply-chain-oriented businesses. That said, the concept of lead time can also be applied in other areas as well, such as, any businesses or projects that are product-oriented or service-oriented.
In order to better understand the concept, we can look into its application in different scenarios.
Application of Lead Time in Different Types of Business Operations
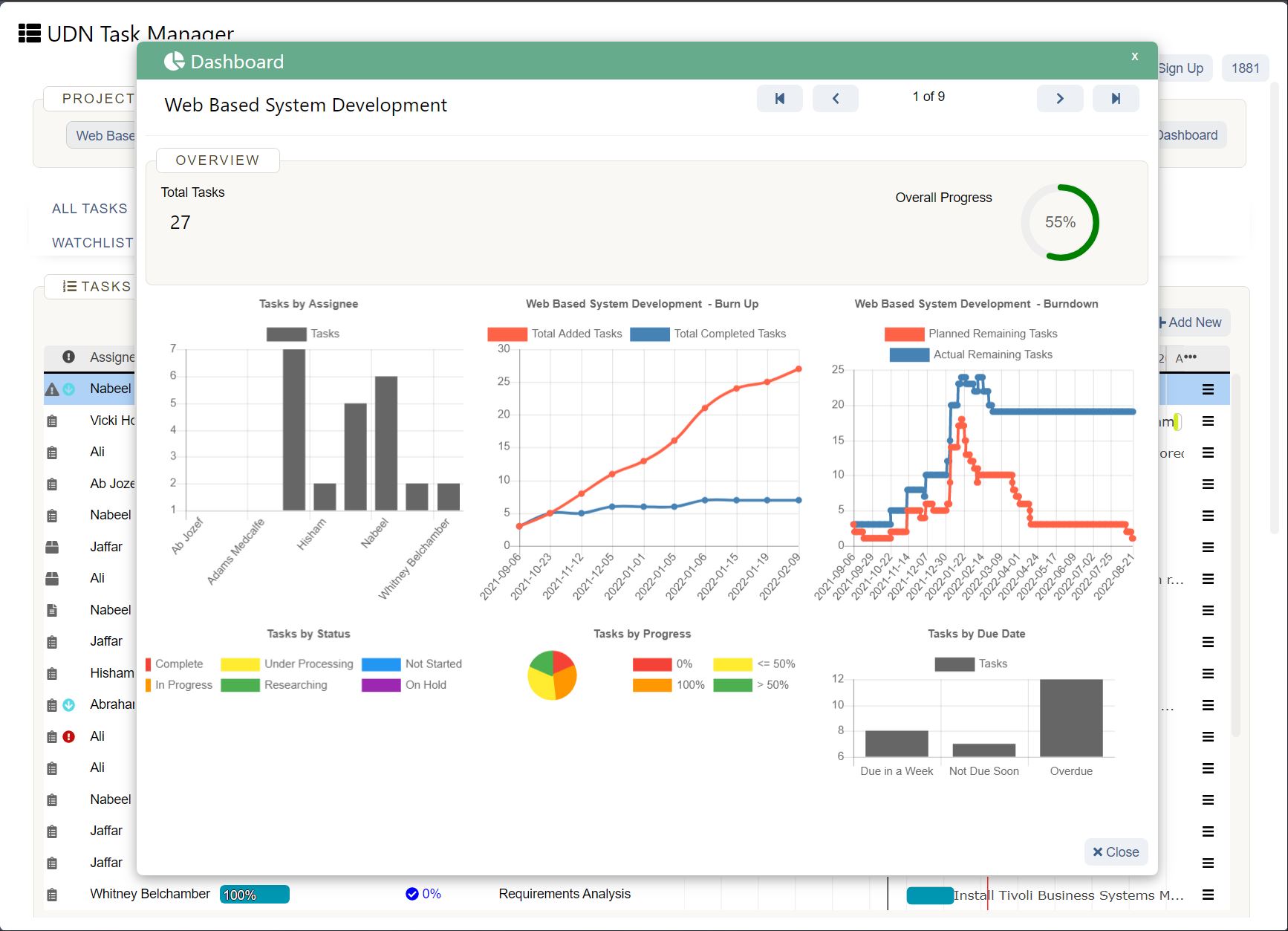
For a business keeping inventory or manufacturing goods, it is vital to have a seamless flow of supplies coming in and finished products being delivered to the clients.
Lead time, in this case, refers to the time taken for a supplier to have the consignment prepared and set for delivery (supply chain). For example, a clothing business may take up to 4 days to have a customized printed t-shirt ready for delivery, and 2 days for shipping the package.
The time period of 4 days would count as the time to be considered since shipping is usually not considered when calculating lead time in the supply chain. This does not apply to manufacturing businesses though. In that case, the assessment of lead time would include the time it has taken for the raw materials to be processed into the final product, including the time it has taken to be delivered to the client.
In terms of a B2C (business to consumer) company, it is vital to minimize any lag that might arise between the time the order is placed by the customer and the time it takes for them to receive the order. This is referred to as order lead time.
While in project management, it refers to the time allotted to either finishing an individual task or completing the entire team’s projects.
How is lead time measured?
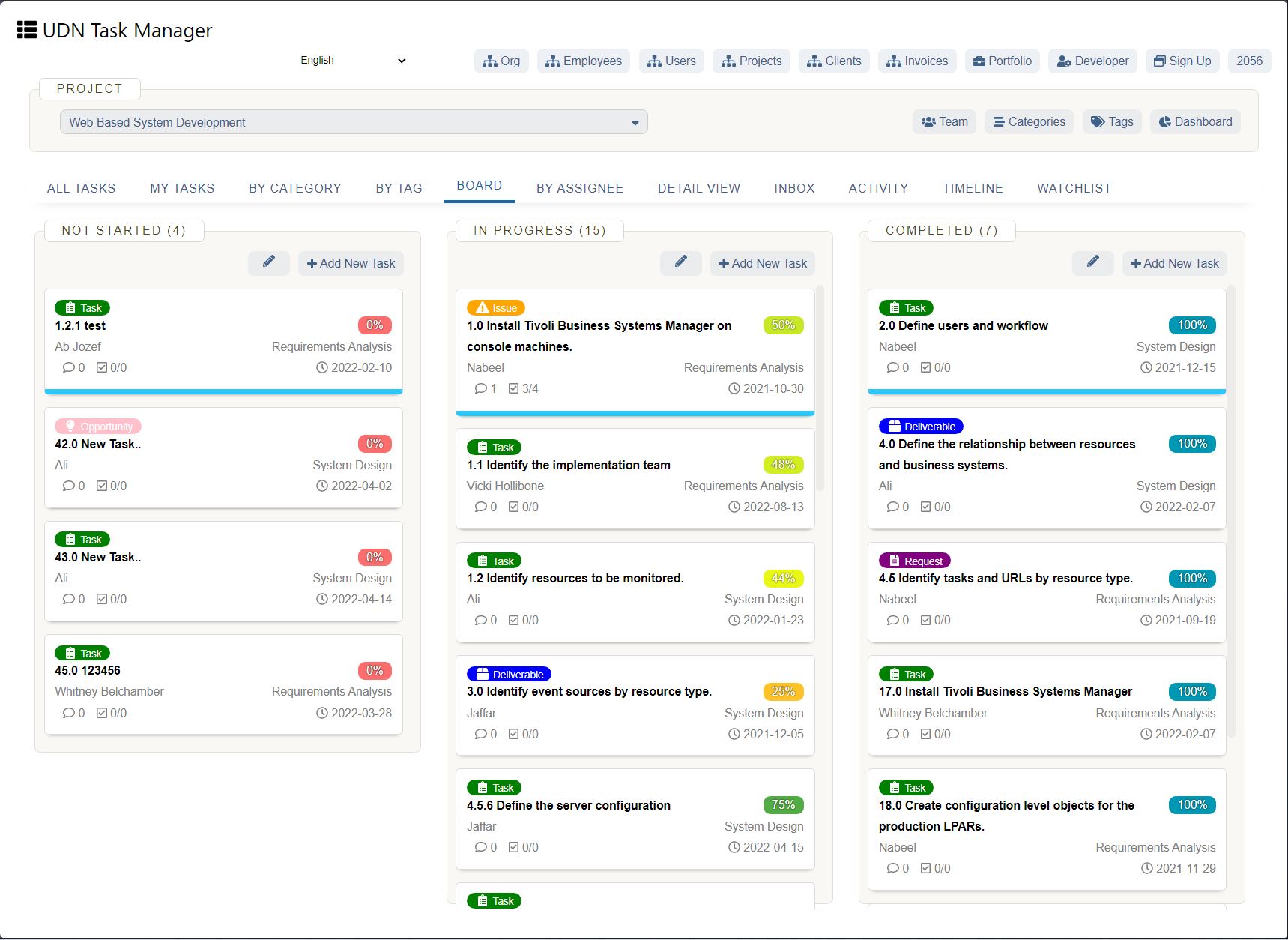
Measuring lead time for any type of business operation is a relatively simple task, as long as you know what variables are involved in the equation. The variables that collectively make up lead time are as follows:
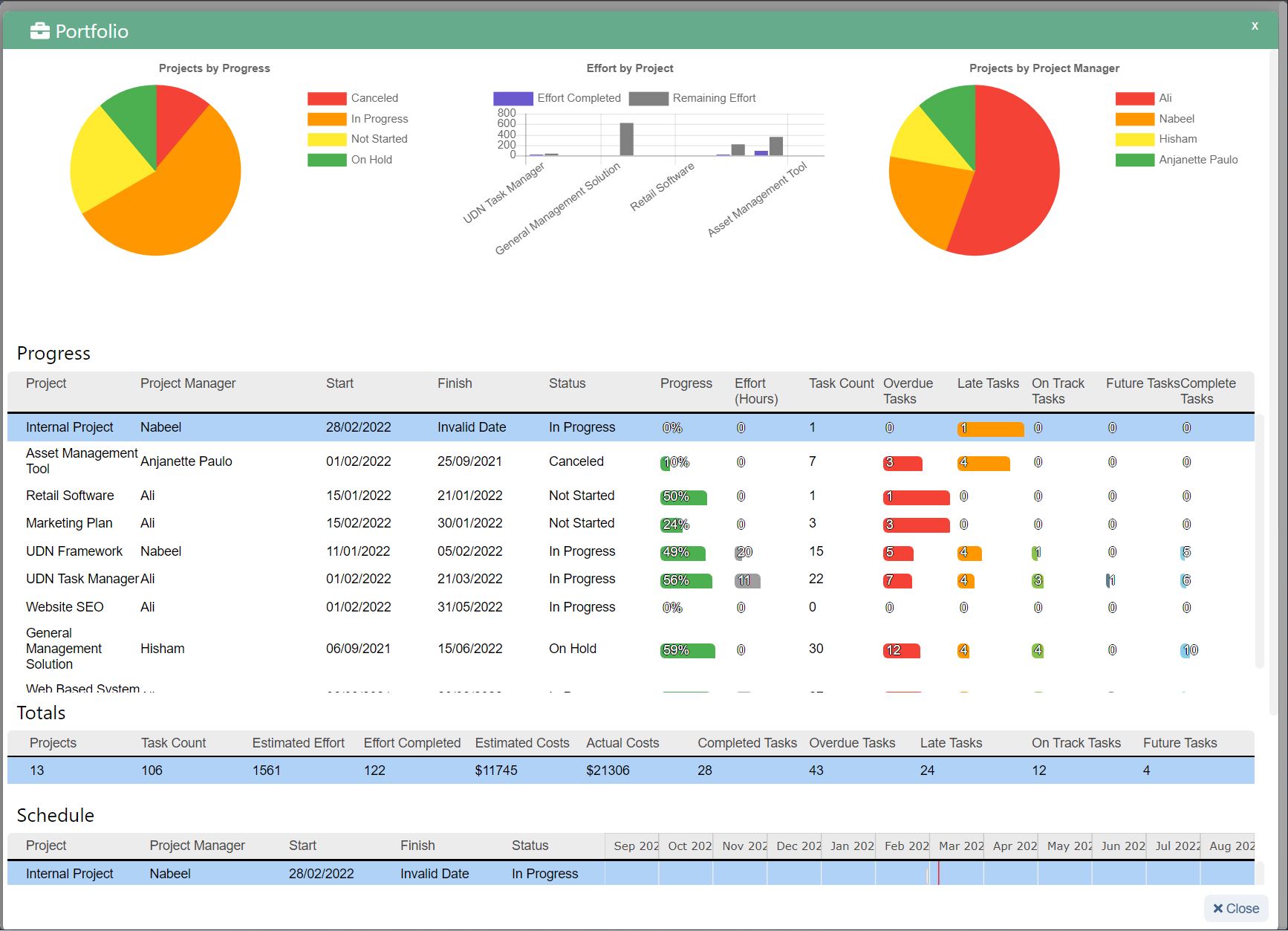
Procurement time refers to the duration of time it takes to get resources ready and available for any new task or order. These resources can either be in form of raw material, final finished goods, or even human talent.
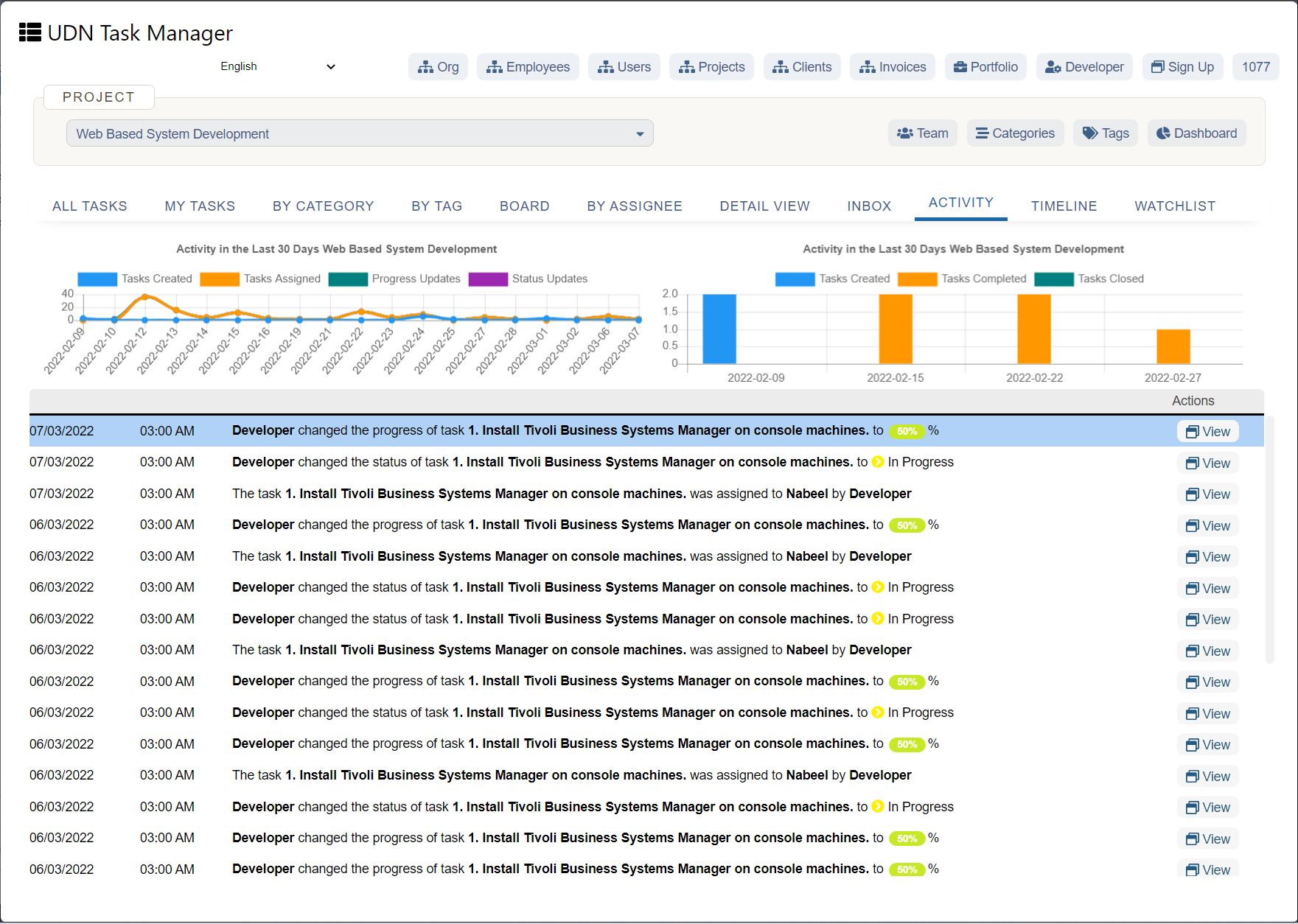
Manufacturing time refers to the duration of time taken to convert the raw material into a ready-to-deliver product after procurement is done. This of course does not apply to all kinds of business models.
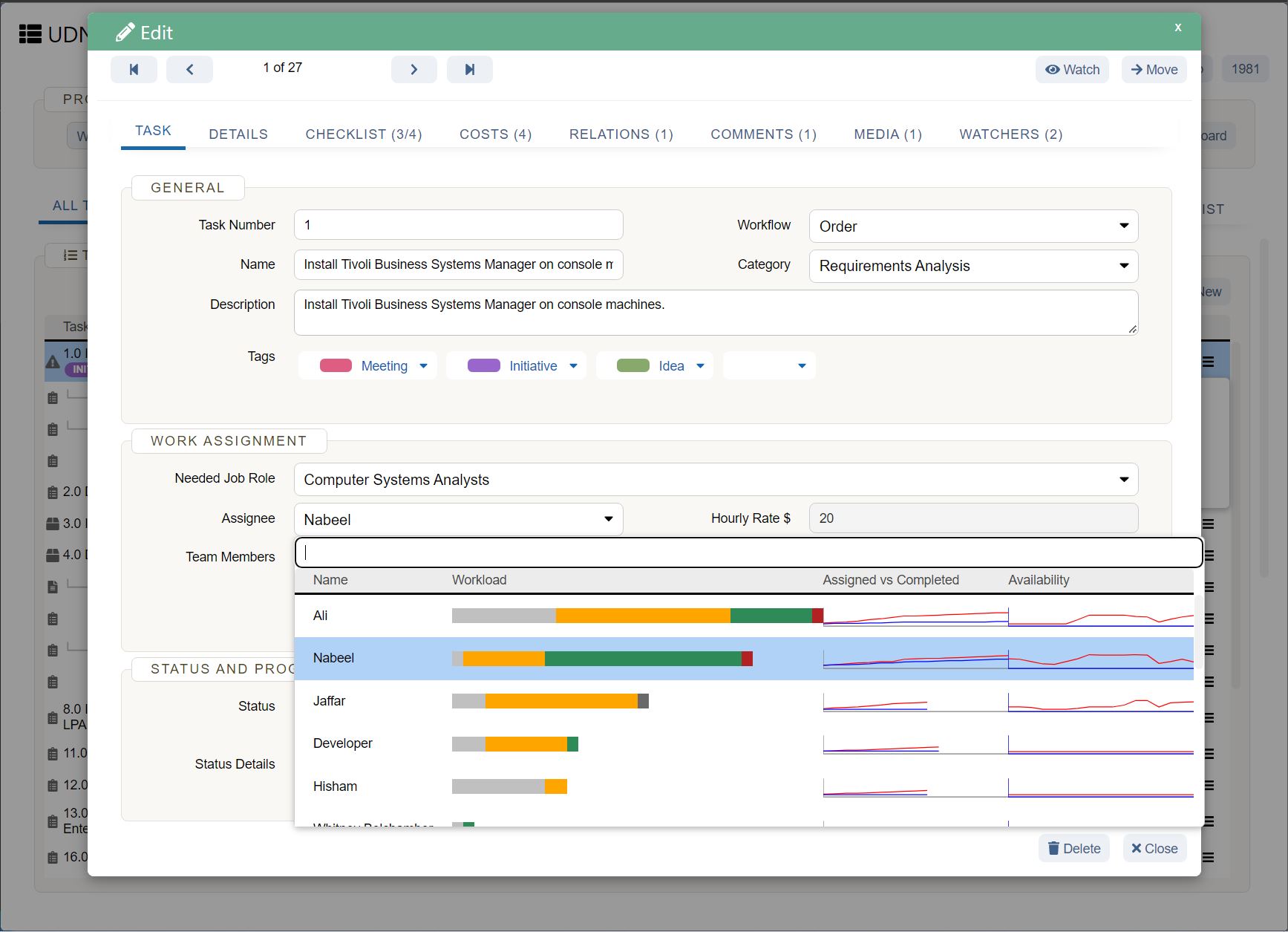
Shipping time refers to the time it takes to ship off the ready product from the manufacturing location to the client.
We’ll now look at how these variables combine to make the formula for calculating lead time .
Lead time = Procurement time + Manufacturing time + Shipping time
Let us apply this formula in a practical example for both supply-chain-related operations and project management-related businesses.
Typically, in a supply-chain business, all the variables are included. Let’s assume it takes three days to procure the supplies/materials, one day to pack the final package, and two days to ship the final packaged product to the client. This would mean the lead time is 3+1+2 i.e., 6 days.
On the other hand, for a project-management-oriented business, let’s take the example of a marketing team making and delivering an advertising budget report.
In this case, procurement time can be referred to as the duration of time taken to put together a team and assign duties, this could be three days. Manufacturing time can be referred to as the time taken to research and actually get the budgeting report made; let’s say it was ten days. In the case of project management shipping time is an irrelevant variable. This would mean the lead time calculation would be 3+10= 13 days.
Importance of Calculating and Optimizing on Lead Time

Now that we have discussed what lead time is and how to measure it, it is also important to understand the significance of this concept.
Companies and individual businesses across the world use the concept of lead time to eliminate inefficiencies, delays in processes, and sidestep any customer dissatisfactions that might arise.
There are numerous aspects in which optimizing lead time can improve the business’s efficiency.
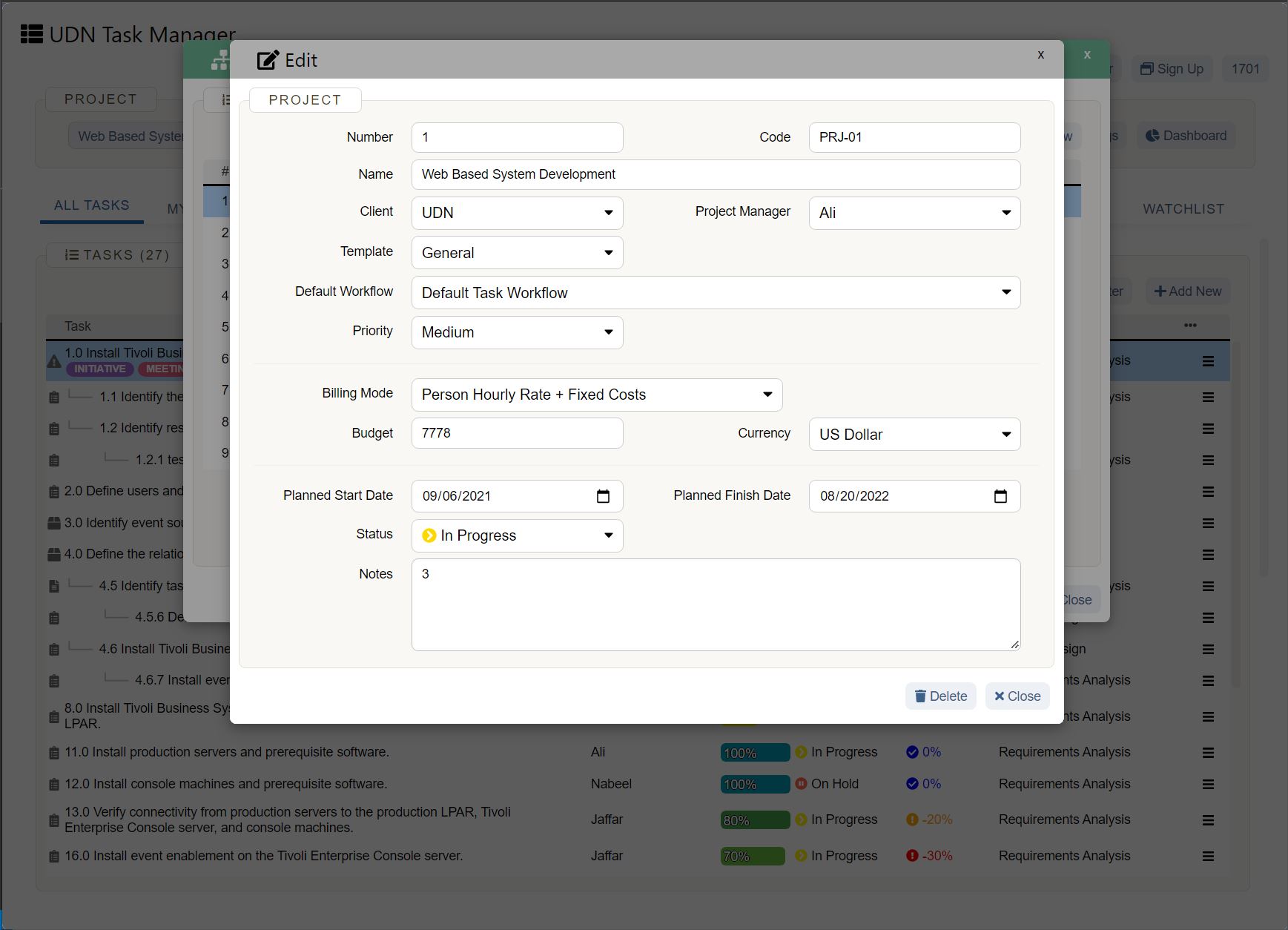
The shorter one’s lead time is, the faster their delivery time. For a customer-centric business, this fast service is grounds for a major competitive edge over other companies.
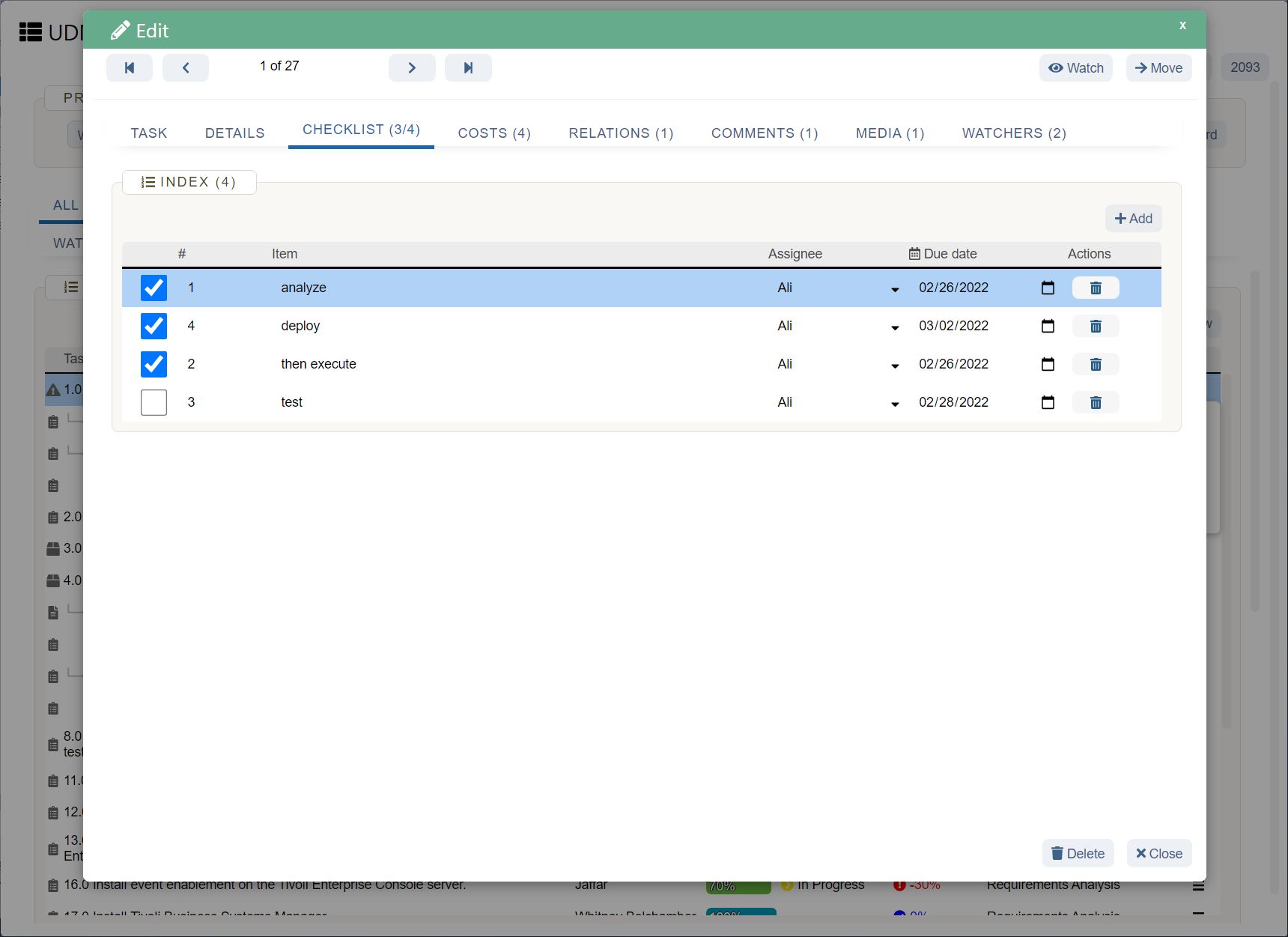
If optimizing the lead time gives you faster service or delivery time, you are bound to have a better-satisfied client base, with greater chances of having loyal customers and improved prospects of increasing future revenues.
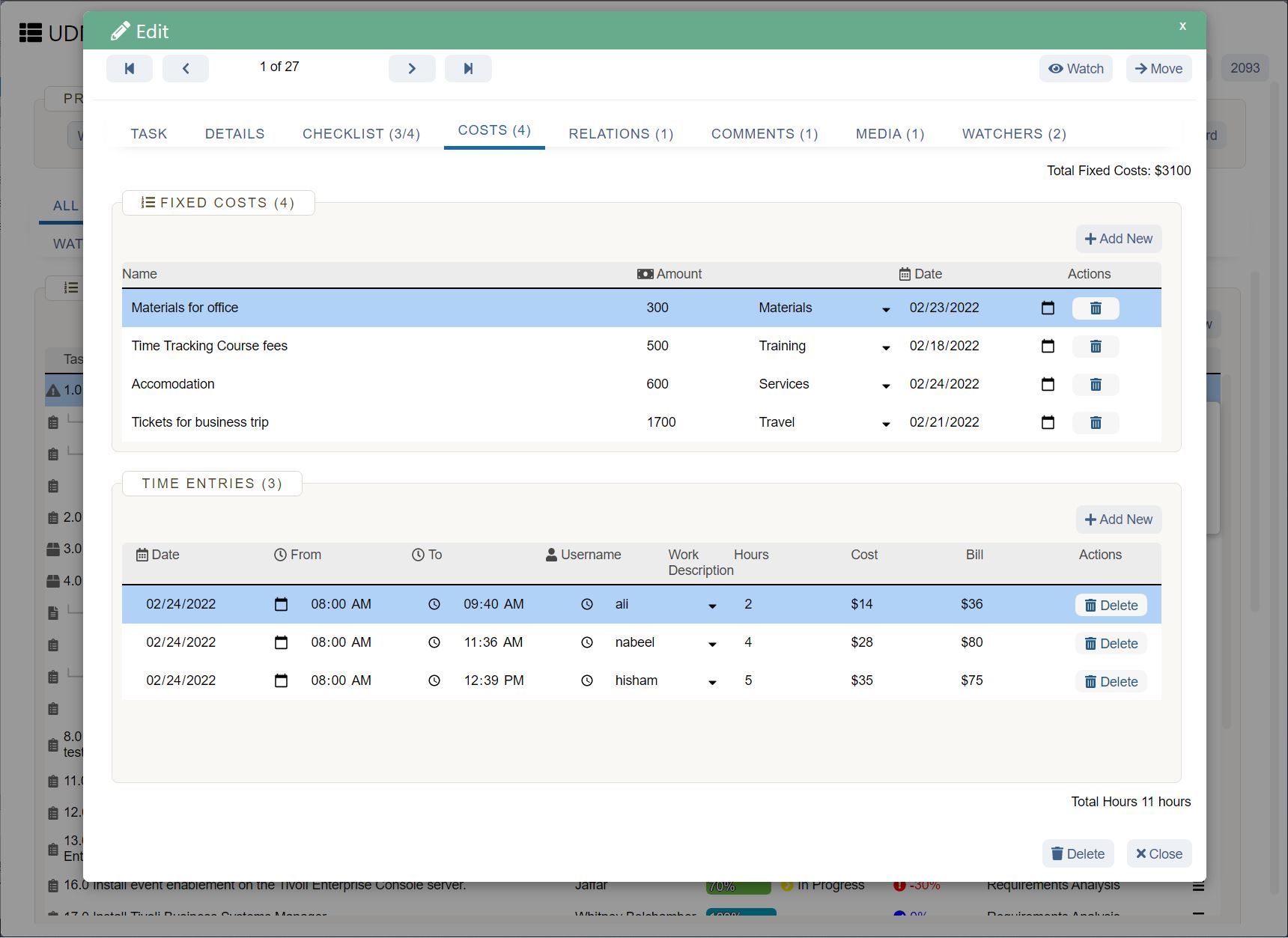
Downtime and wastages are all inefficiencies that might befall a team or a company when performing a certain task. These might include time lags between processes due to any given reason or even under or overutilization of any resources.
Once you work with the understanding of lead time, it becomes easier for you to work on eliminating all these wastages and inefficiencies, in turn bringing your costs down.
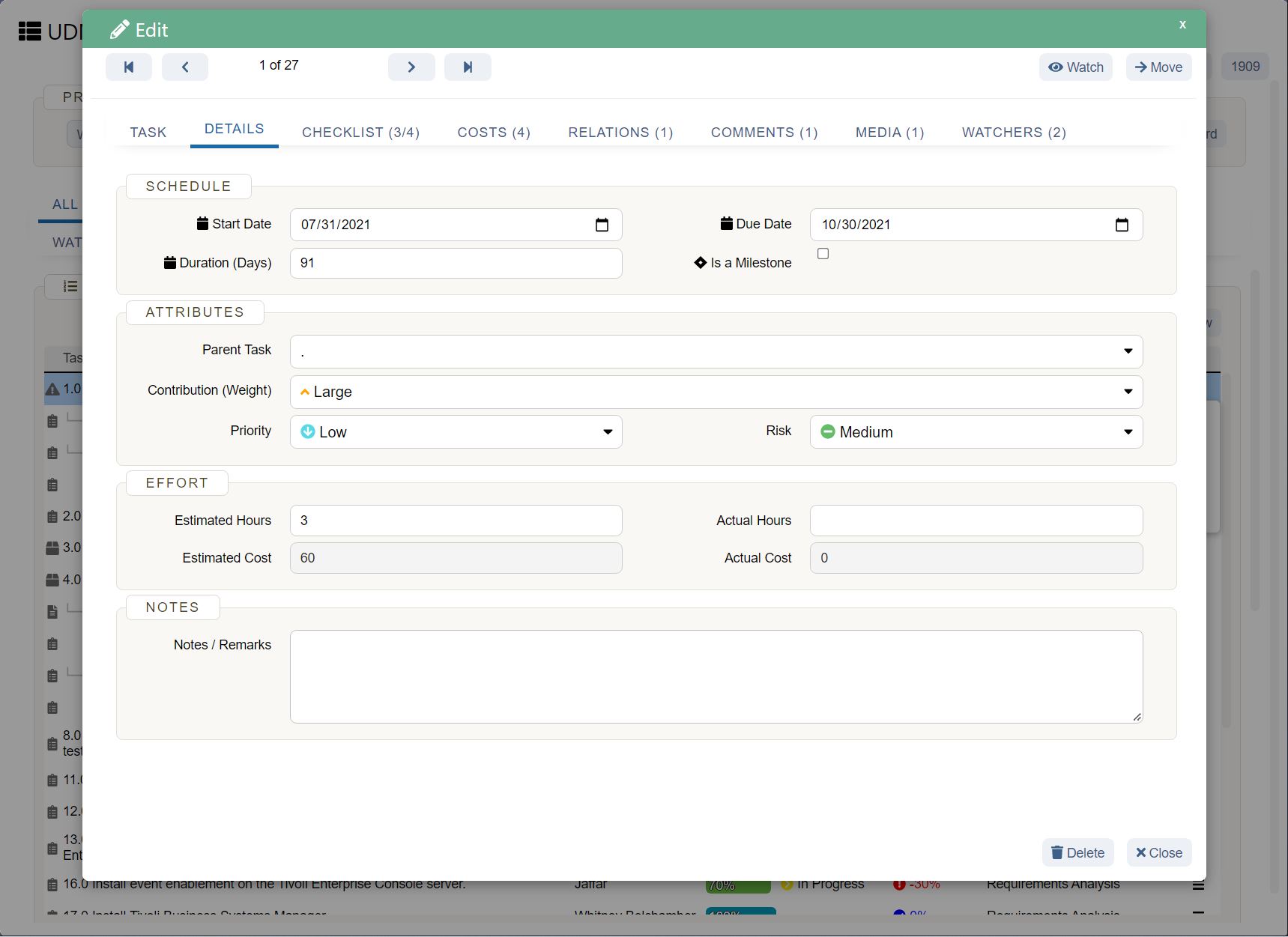
Continuing the idea of eliminating downtime and wastage; if there is any reduction in such inefficiencies, it is bound to be reflected in the overall rate of productivity.
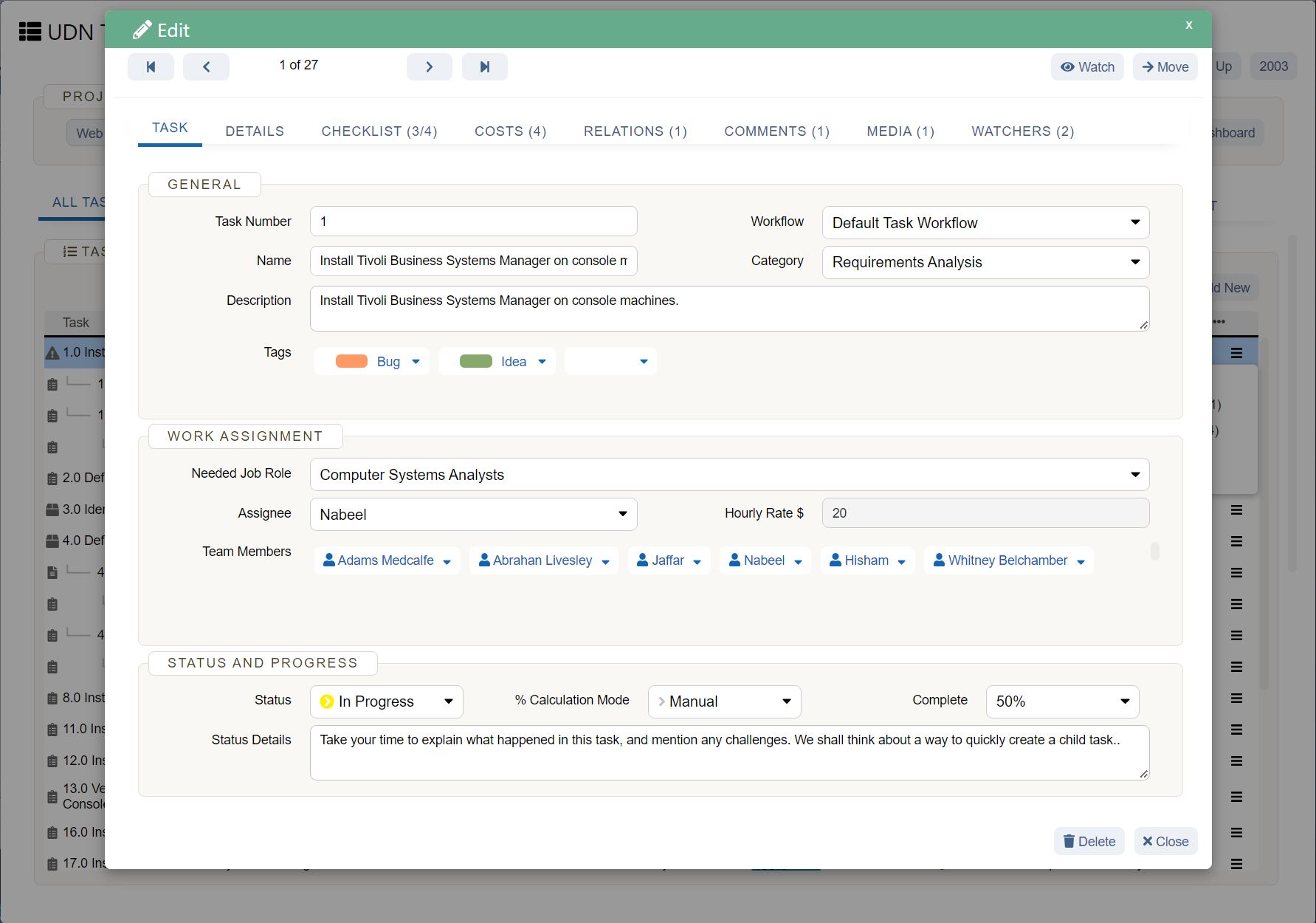
In many cases, especially when you consider project management examples , there are instances where the flow of a project depends on the completion of one task before any of the following can be started hence interrupting the flow of the entire project. Correctly estimating lead time also helps eliminate these dependencies.
Example of Lead Time in Inventory Management
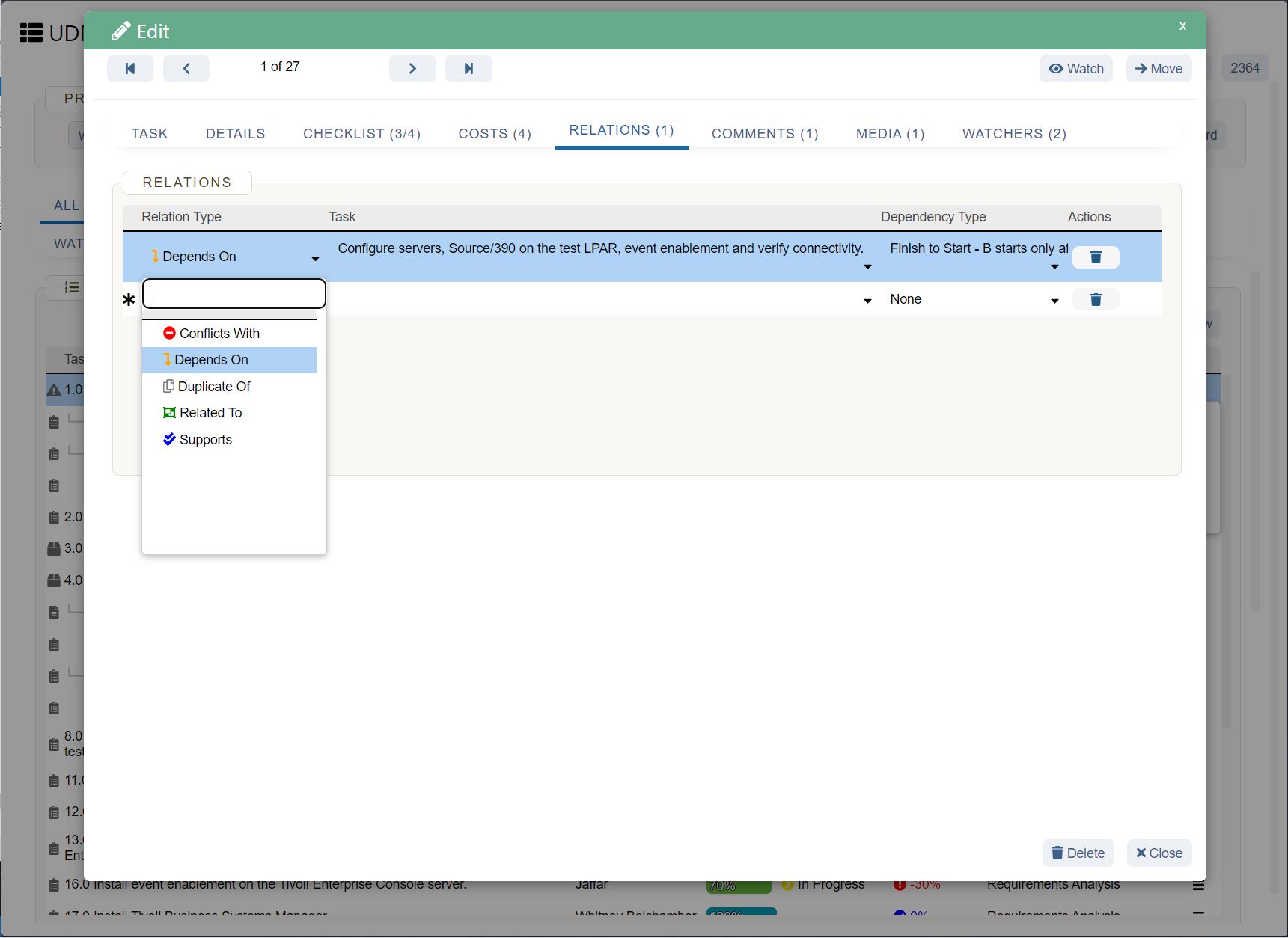
Let’s now look at an example of how optimizing lead time can help with inventory management.
Let’s look at an example of a wholesale seller. He has one round of ordered inventory being turned over in sales. He has to know the optimal time to place the order for new stock before he runs out of the current one in sales rotation.
This is known as knowing your reordering point and it helps in eliminating wastage of time in terms of having no stock to sell until it’s reordered again.
Reordering Point (ROP) is a simple calculation for which one needs to know the time taken for an order to be delivered by the supplier (lead time), the amount of stock one needs to keep as a contingency to avoid running out of stock ( safety stock ), and daily average sales of the item being sold or ordered.
Once all these are known we simply have to multiply daily average usage with the lead time to calculate ROP. In case your business model requires you to keep safety stock, you add the value of safety stock to the formula; but if you deal with more custom ordered items like perfumes, make-ups, jewelry, etc there is no need for accounting in safety stock.
It’s ideal to have multiple suppliers for the same item as a backup, to avoid any mishaps in case one supplier fails to deliver on time, causing your business to be disrupted.
Conclusion
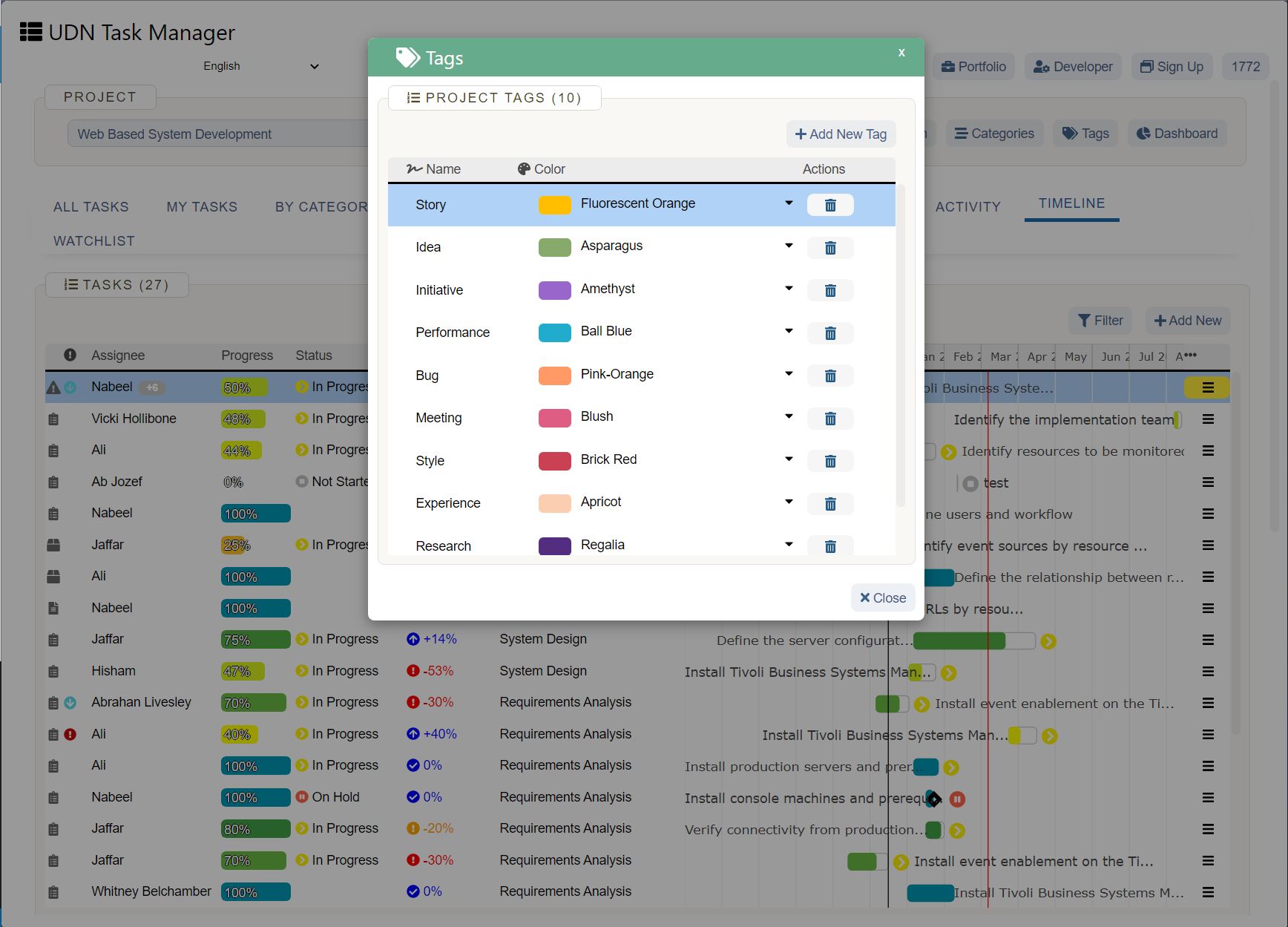
And there you have it! A guide to getting you started on knowing and calculating lead times for your business, organization, or your next project.
Remember, you need to take the time to calculate such measurements to provide your customer and clients with the best and most efficient experience with your product or service possible.
To take away some of the hassles of calculating lead times and communicating with your team about manufacturing or shipping times you should consider trying UDN Task Manager .
UDN Task Manager is a versatile project management tool with a versatile feature-set that offers teams from all different industries the ability to stay organized and keep all their affairs under one platform.
It also offers teams the ability to communicate and collaborate with ease with meeting management, file sharing and storage, and more.
Check out the available tools that UDN Task Manager has to offer or get in touch with one of our sales representatives to get a demo of the product and see how you can use the features for the better working of your team.
You May Also Like: