Lessons Learned from Project Failure at Denver International Airport: Why Checking Bags is Still a Pain
We regularly review major projects to extract valuable lessons and pass on the knowledge so that everyone can benefit. One failed project we recently took an interest in is Denver International Airport's luggage handling system.
I was compelled to study this project because checking bags at the airport is still one of my biggest fears. My eye twitches just thinking about it. You can never predict how long check-in lines will be, suitcases are lost daily, and human baggage handlers have a tendency to manhandle their wards. We have probably all wondered why airports haven't come up with a better system by now.
The Failed Project of Denver International Airport
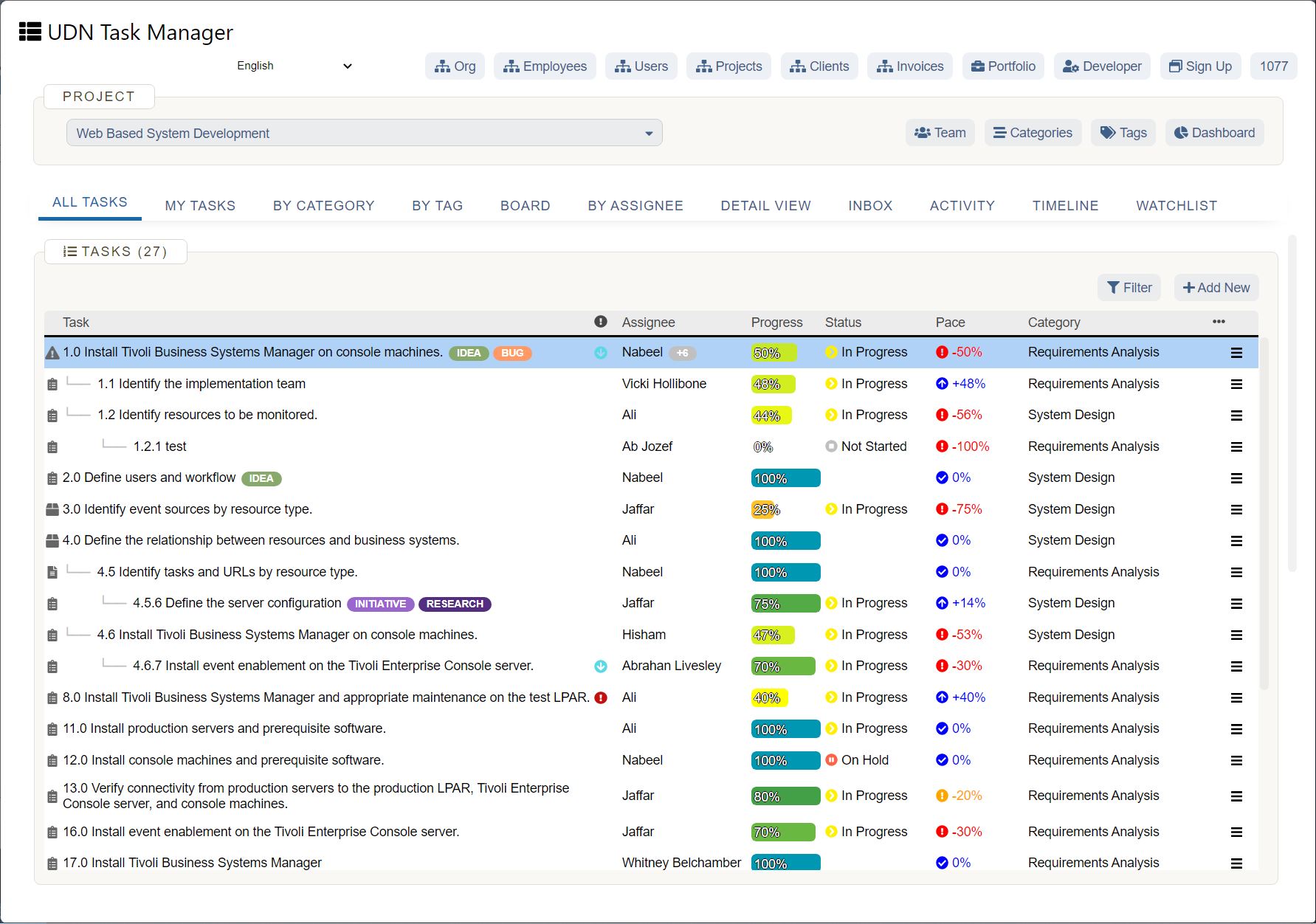
It's not that airports haven't tried to fix the baggage system. When construction started on the new Denver International Airport, it was supposed to come with a brand-new automated system for handling luggage travel and transfers. The goal was to replace the standard reliance on manual labor with a fully-automated baggage system that would also integrate all three terminals. It would reduce aircraft turn-around time for faster service to travelers.
But the project went 16 months past its hard deadline, cost the city $560 million over budget, and performed just a fraction of its original automation goals. Instead of integrating the three concourses and all airlines, it was only used at one concourse, for one airline, for outbound flights only. The project team had to resort to building a second, manual labor system for all other baggage operations. And after valiantly attempting to use the system for 10 years, the only airline that actually adopted the system finally bowed out due to high maintenance costs.
The project ended in spectacular failure — and from their mistakes, we stand to learn a lot about project communication, scope creep , and poor project definition .
Want a tool to improve your project management ? Start your free UDN Task Manager trial today!
3 Lessons We Should Learn from Denver
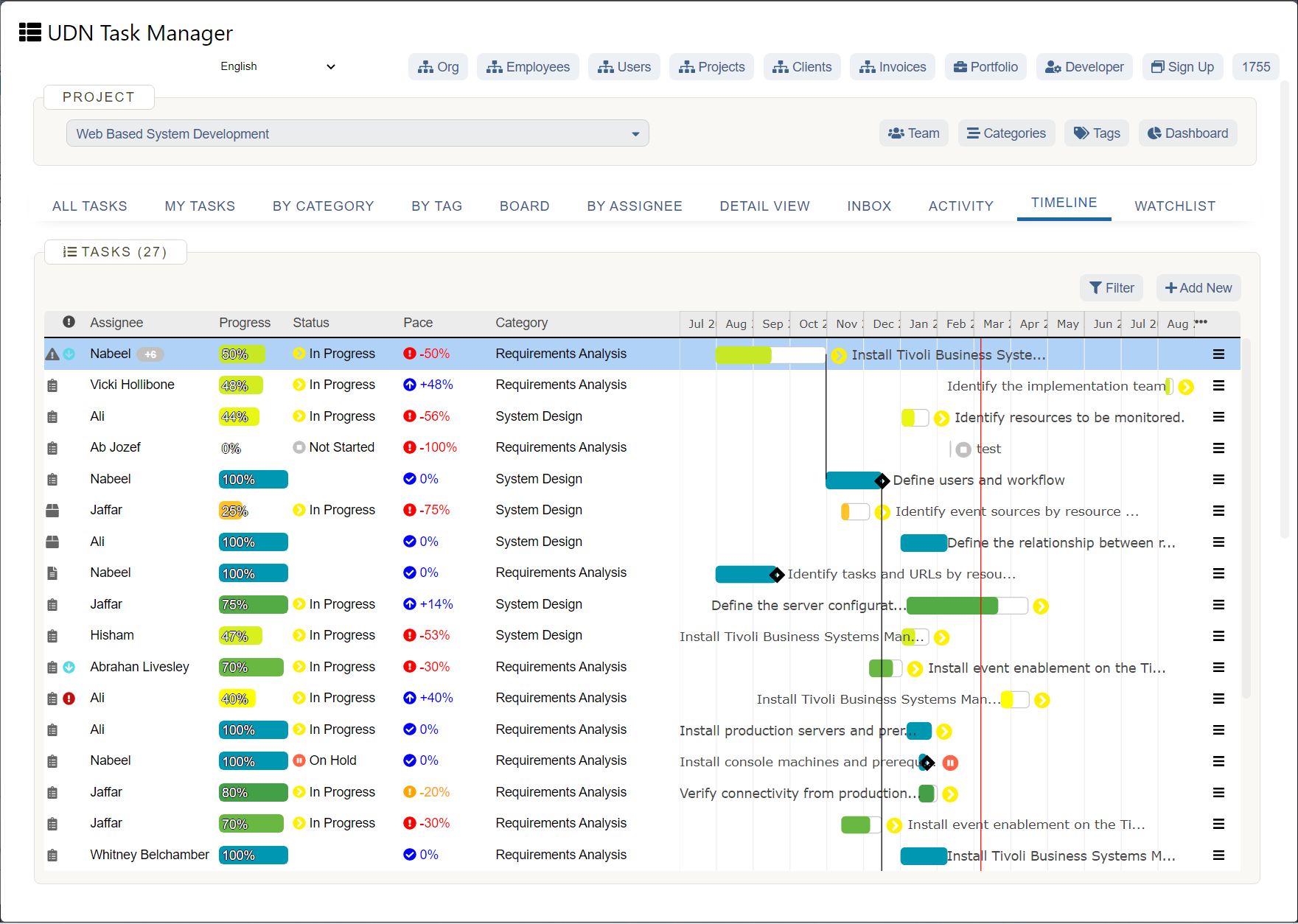
1. Listen when people say, "This isn't going to work."
Warning #1: After airport construction started, the City of Denver hired Breier Neidle Patrone Associates to evaluate if the proposed baggage system project was feasible. The company flat-out stated that the plan was too complex
Warning #2: A similar, simpler project in Munich took a full two years to be completed, followed by six months of 24/7 testing prior to the actual launch. The larger, much more complex Denver International Airport system was due to open in a little over two years. Which means that Denver International Airport was trying to cram a very complicated project into a very short timeline
Warning #3: When the airport began accepting bids on the new luggage system project, only three companies submitted proposals. Of those proposals, none of them predicted they'd be able to finish the project within the allotted timeframe. The city rejected all three bids, and instead approached a fourth company, BAE Systems, to convince them to take on the superhuman project; again, without changing the proposed timeline
Warning #4: Senior managers at BAE Systems expressed initial misgivings about the project's complexity. They estimated a 4-year timeline instead of 2 years, but the concern was ignored
Four ignored warnings later, nothing had changed. If the City of Denver or the project team had heeded any of these caution flares regarding project complexity and tight deadlines, they would have changed their timeline or scaled back their goals. Instead they barreled ahead, and as a result their project went far past deadline, cost millions of extra dollars, with the final product a disappointing shadow of its original design.
If the project failure of Denver International Airport teaches you only one thing, it's this: pay attention to the flashing red lights
2. Don't wait to involve all parties affected by the project
While BAE Systems and the airport's larger project management team were the steamrollers on the project, they were ultimately not the parties affected by the outcome. Airlines renting space in the airport would be most impacted by the outcome of the automated baggage system. Yet they were not brought into the planning discussions. These key stakeholders were excluded from the initial decision-making
Once the airlines were finally asked for their opinions, they required major changes
By waiting to approach stakeholders, the project team wasted time and money
It is essential that we include stakeholders from Day 1 to avoid wasting time and money. Don't make the same mistake of waiting until halfway through a project to collect vital requirements.
3. Beware of "Big Bang" projects meant to change the world
Another project complication was the decision to go with an all-at-once "Big Bang" rollout to all three concourses, as opposed to slower, incremental rollout. In an article dissecting the problems with Denver International Airport's baggage system project plan , Webster & Associates LLC, an IT consulting company, said that this was one of the biggest project flaws. BAE Systems should have tested the new automated system in sections to make sure it would work before implementing it throughout the rest of the airport.
This project was the first attempt at an automated system of this size and complexity, and was meant to change the way that airports handled baggage. They wanted instant, large-scale success. Instead, the final product fell short of everyone's expectations.
The best way to get big results is to first ensure you can create a successful minimal viable product
Project Failure is Not Fatal
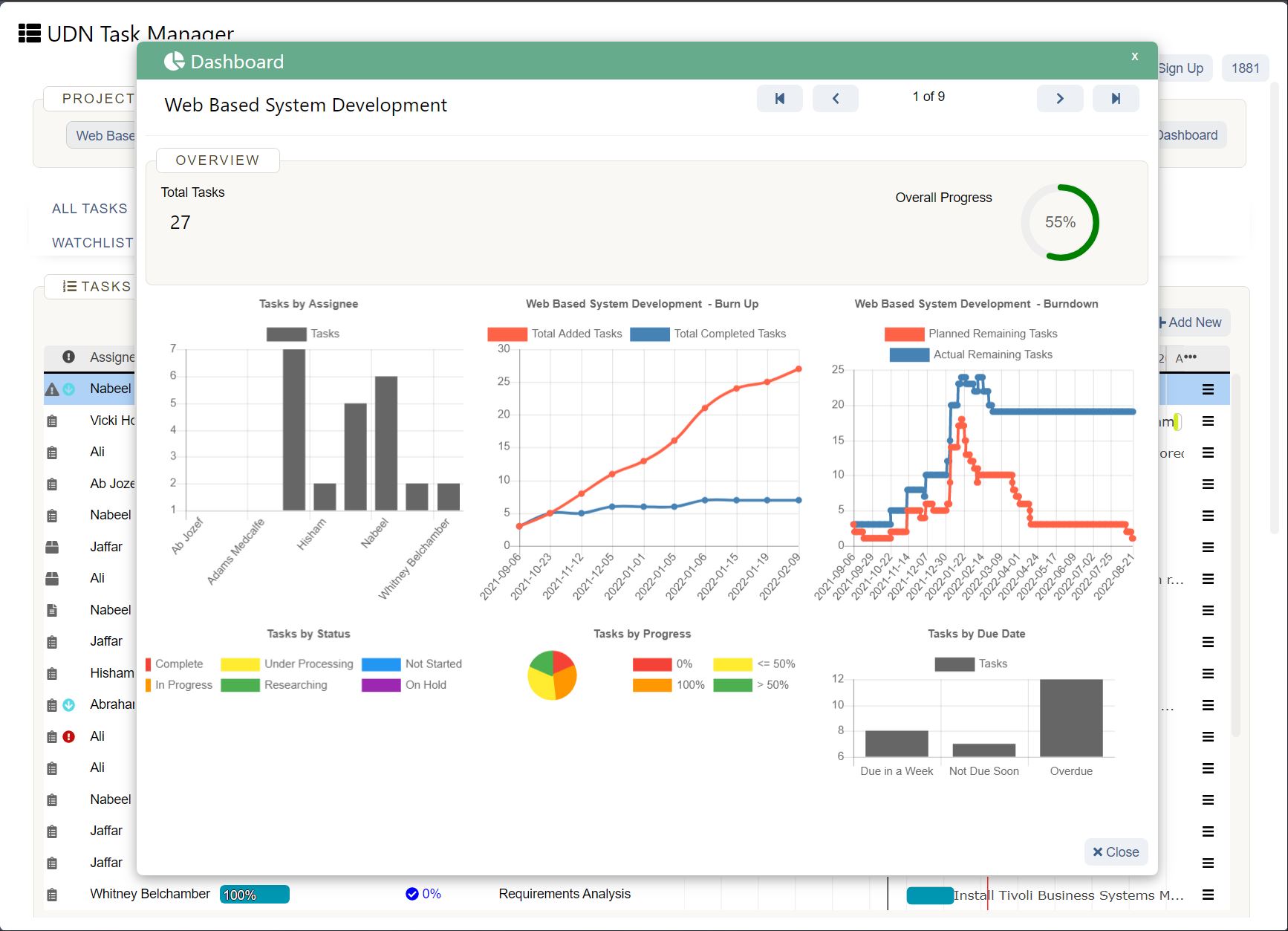
Although the automated baggage system failed, today the Denver International Airport is fully functional. I've even taken my skis through their airport without issue. And as long as we learn valuable lessons from their mistakes, we shouldn't consider this project a complete failure — just a painful boo-boo.
Next time you're working on a project, remember these three lessons and avoid facing the same fate as Denver International Airport:
1. Watch for red flags, and heed the warnings of experts. 2. Involve all project stakeholders from Day 1. 3. Take small steps to successfully reach the end goal.
Good luck on your next projects and next flights!
Related Articles:
• 10 Reasons Projects Fail: Lessons from the Death Star • 3 Kinds of Data to Help Avoid Project Management Failure
Sources: http://calleam.com/WTPF/?page_id=2086 , http://calleam.com/WTPF/content/uploads/articles/DIABaggage.pdf , http://www.computerworld.com/article/2556725/it-project-management/united-axes-troubled-baggage-system-at-denver-airport.html , http://archive.gao.gov/t2pbat1/154219.pdf , http://www.eis.mdx.ac.uk/research/SFC/Reports/TR2002-01.pdf